Advanced, integrated energy solutions
Building on our expertise in demand-side management.
The clean energy transition requires a comprehensive approach. We're constantly investing in our portfolio of energy software and solutions to guide utilities through complex, connected challenges.
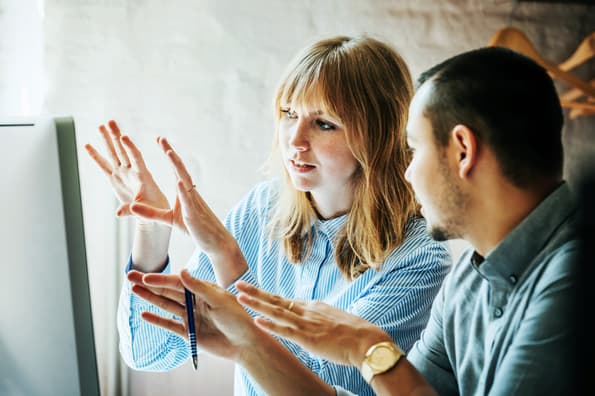
Real results, real progress
Driving energy impact at scale.
Resource Innovations provides end-to-end energy transformation software and services that improve customer engagement, boost operational efficiency, and deliver superior outcomes.
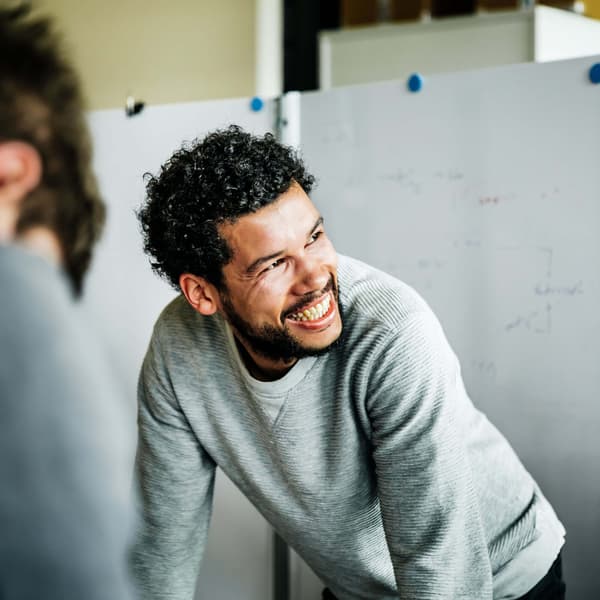
Making clean energy more available, accessible, and affordable.
Resource Innovations has the people, passion, and scale to lead the energy transition.
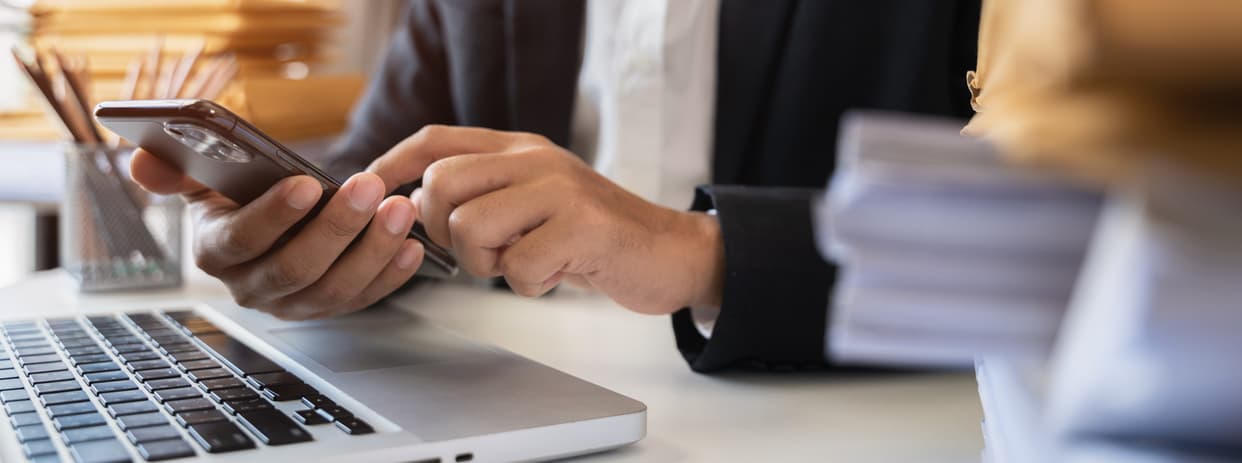
Free e-commerce webinar recording
From Vision to Value: Building a Utility Marketplace That Delivers Real Impact
Unlock the secrets to a thriving digital marketplace! Watch Resource Innovations' webinar recording to explore Snohomish PUD's transformative e-commerce journey.
Accelerating the clean energy transition.
Leading utilities, government agencies, and system operators depend on Resource Innovations' expertise to meet their sustainability goals and improve customer satisfaction.